Commissioning tests of protection relays at site (before set to work)
Installation of protection relays
Installation of protection relays at site creates a number of possibilities for errors in the implementation of the scheme to occur. Even if the scheme has been thoroughly tested in the factory, wiring to the CTs and VTs on site may be incorrectly carried out, or the CTs/VTs may have been incorrectly installed.
The impact of such errors may range from simply being a nuisance (tripping occurs repeatedly on energisation, requiring investigation to locate and correct the errors) through to failure to trip under fault conditions, leading to major equipment damage, disruption to supplies and potential hazards to personnel.
The strategies available to remove these risks are many, but all involve some kind of testing at site. Commissioning tests at site are therefore invariably performed before protection equipment is set to work. The aims of commissioning tests are:
- To ensure that the equipment has not been damaged during transit or installation
- To ensure that the installation work has been carried out correctly
- To prove the correct functioning of the protection scheme as a whole
The tests carried out will normally vary according to the protection scheme involved, the relay technology used, and the policy of the client. In many cases, the tests actually conducted are determined at the time of commissioning by mutual agreement between the client’s representative and the commissioning team.
The following tests are invariably carried out, since the protection scheme will not function correctly if faults exist.
- Wiring diagram check, using circuit diagrams showing all the reference numbers of the interconnecting wiring
- General inspection of the equipment, checking all connections, wires on relays terminals, labels on terminal boards, etc.
- Insulation resistance measurement of all circuits
- Perform relay self-test procedure and external communications checks on digital/numerical relays
- Test main current transformers
- Test main voltage transformers
- Check that protection relay alarm/trip settings have been entered correctly
- Tripping and alarm circuit checks to prove correct functioning
- Secondary injection test on each relay to prove operation at one or more setting values
- Primary injection tests on each relay to prove stability for external faults and to determine the effective current setting for internal faults (essential for some types of electromechanical relays)
- Testing of protection scheme logic
Insulation resistance tests
All the deliberate earth connections on the wiring to be tested should first be removed, for example earthing links on current transformers, voltage transformers and DC supplies. Some insulation testers generate impulses with peak voltages exceeding 5kV. In these instances any electronic equipment should be disconnected while the external wiring insulation is checked.
The insulation resistance should be measured to earth and between electrically separate circuits. The readings are recorded and compared with subsequent routine tests to check for any deterioration of the insulation.
The insulation resistance measured depends on the amount of wiring involved, its grade, and the site humidity. Generally, if the test is restricted to one cubicle, a reading of several hundred megohms should be obtained. If long lengths of site wiring are involved, the reading could be only a few megohms.
Protection relay self-test procedure
Digital and numerical relays will have a self-test procedure that is detailed in the appropriate relay manual. These tests should be followed to determine if the relay is operating correctly.
This will normally involve checking of the relay watchdog circuit, exercising all digital inputs and outputs and checking that the relay analogue inputs are within calibration by applying a test current or voltage.
For these tests, the relay outputs are normally disconnected from the remainder of the protection scheme, as it is a test carried out to prove correct relay, rather than scheme, operation.

To shorten testing and commissioning times of SIPROTEC relays, extensive test and diagnostic functions are available to the user in DIGSI 5
Unit protection schemes involve relays that need to communicate with each other. This leads to additional testing requirements. The communications path between the relays is tested using suitable equipment to ensure that the path is complete and that the received signal strength is within specification. Numerical relays may be fitted with loopback test facilities that enable either part of or the entire communications link to be tested from one end.
After completion of these tests, it is usual to enter the relay settings required. This can be done manually via the relay front panel controls, or using a portable PC and suitable software.
Whichever, method is used, a check by a second person that the correct settings have been used is desirable, and the settings recorded. Programmable scheme logic that is required is also entered at this stage.

SIPROTEC relay wiring test editor for monitoring and testing of binary inputs, binary outputs and LED (click to expand)
Current transformer tests
The following tests are normally carried out prior to energisation of the main circuits: checking of polarity and current transformer magnetisation curve.
Polarity check
Each current transformer should be individually tested to verify that the primary and secondary polarity markings are correct (see Figure 1).
The ammeter connected to the secondary of the current transformer should be a robust moving coil, permanent magnet, centre-zero type. A low voltage battery is used, via a single-pole push-button switch, to energise the primary winding. On closing the push-button, the DC ammeter, A, should give a positive flick and on opening, a negative flick.

Checking of magnetisation curve
Several points should be checked on each current transformer magnetisation curve. This can be done by energising the secondary winding from the local mains supply through a variable auto-transformer while the primary circuit remains open. See Figure 2.
The magnetising current should then be recorded at similar voltage intervals as it is reduced to zero.
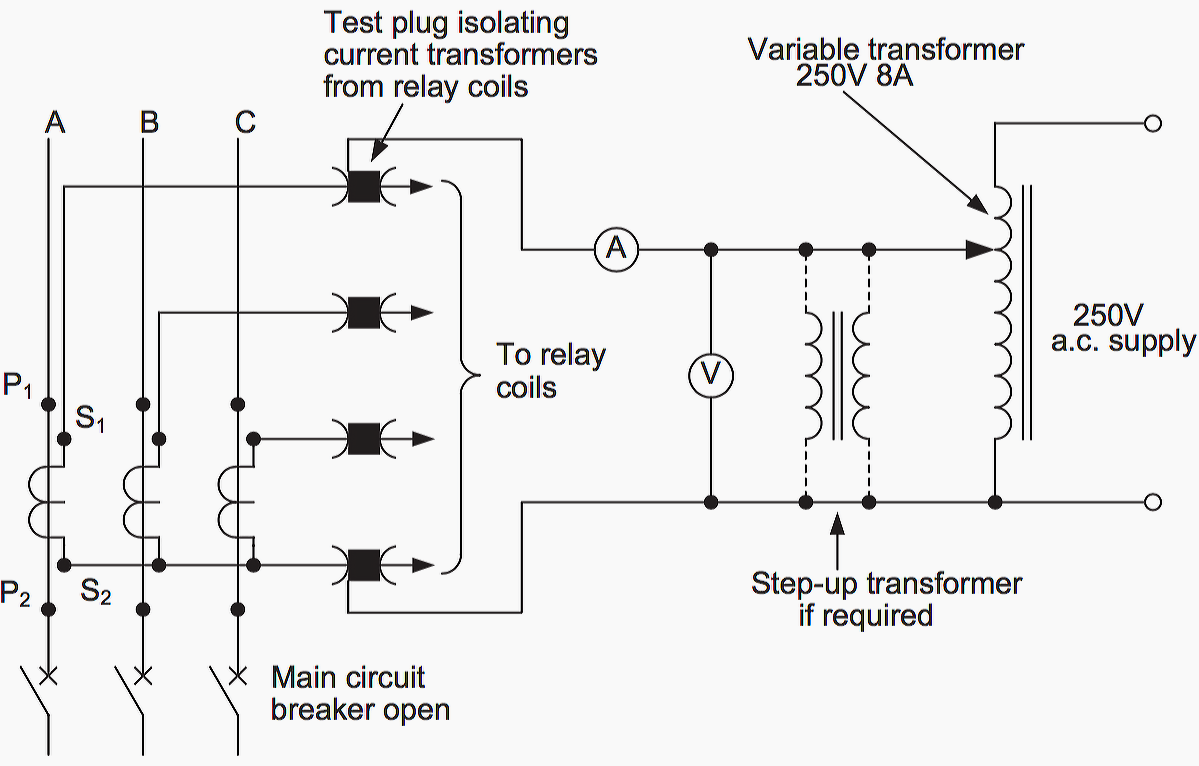
Care must be taken that the test equipment is suitably rated. The short-time current rating must be in excess of the CT secondary current rating, to allow for measurement of the saturation current. This will be in excess of the CT secondary current rating. As the magnetising current will not be sinusoidal, a moving iron or dynamometer type ammeter should be used.
It is often found that current transformers with secondary ratings of 1A or less have a knee-point voltage higher than the local mains supply. In these cases, a step-up interposing transformer must be used to obtain the necessary voltage to check the magnetisation curve.
Voltage transformer tests
Voltage transformers require testing for polarity, ratio and phasing.
Polarity check of voltage transformer
The voltage transformer polarity can be checked using the method for CT polarity tests. Care must be taken to connect the battery supply to the primary winding, with the polarity ammeter connected to the secondary winding. If the voltage transformer is of the capacitor type, then the polarity of the transformer at the bottom of the capacitor stack should be checked.
Ratio check of VT
This check can be carried out when the main circuit is first made live. The voltage transformer secondary voltage is compared with the secondary voltage shown on the nameplate.

Phasing check of VT
The secondary connections for a three-phase voltage transformer or a bank of three single-phase voltage transformers must be carefully checked for phasing. With the main circuit alive, the phase rotation is checked using a phase rotation meter connected across the three phases, as shown in Figure 3 below.
Provided an existing proven VT is available on the same primary system, and that secondary earthing is employed, all that is now necessary to prove correct phasing is a voltage check between, say, both ‘A’ phase secondary outputs. There should be nominally little or no voltage if the phasing is correct.
This can be checked by removing the fuses from phases B and C (say) and measuring the phase-earth voltages on the secondary of the VT. If the phasing is correct, only phase A should be healthy, phases B and C should have only a small residual voltage.
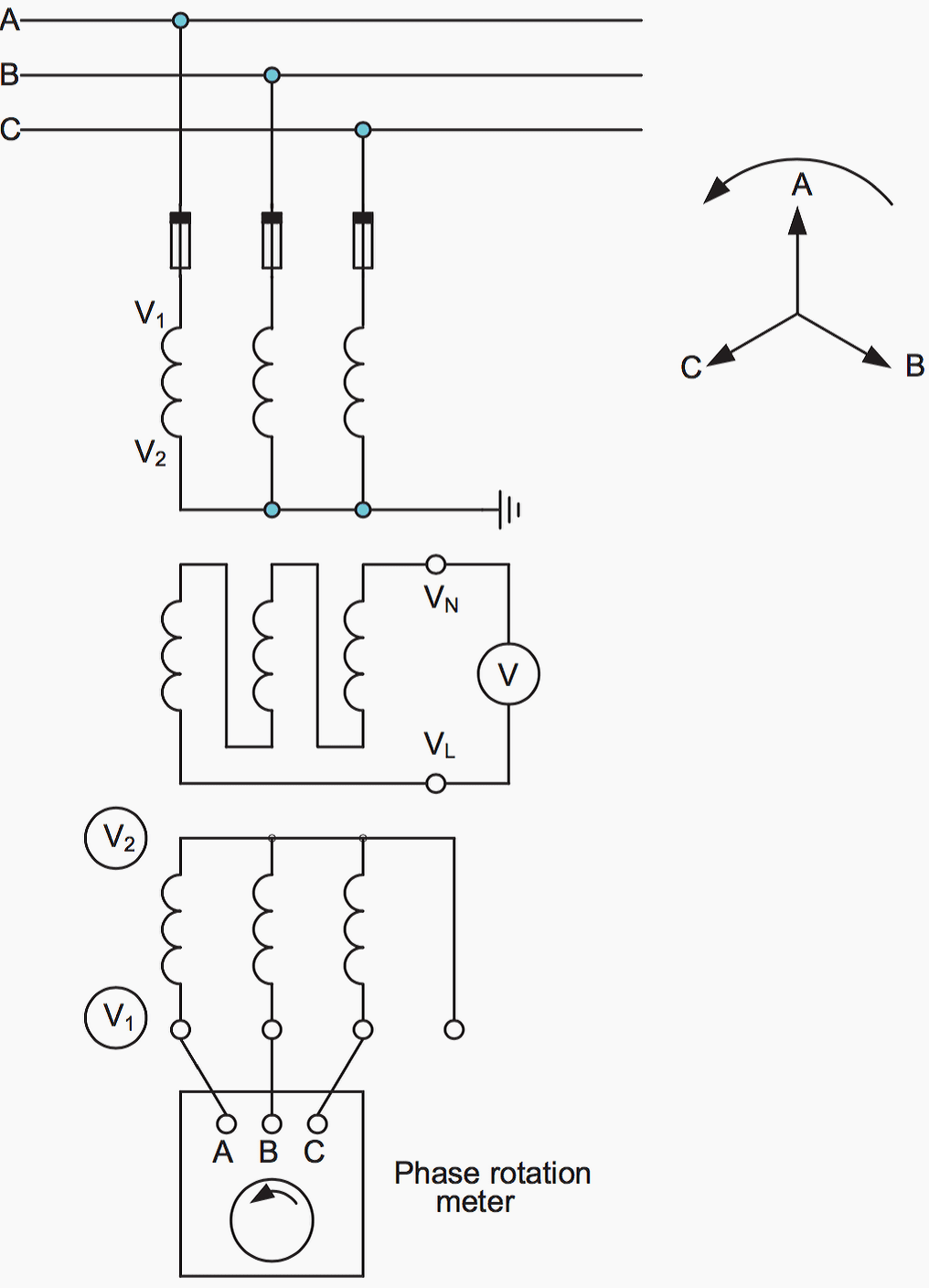
Correct phasing should be further substantiated when carrying out ‘on load’ tests on any phase-angle sensitive relays, at the relay terminals. Load current in a known phase CT secondary should be compared with the associated phase to neutral VT secondary voltage.
The phase angle between them should be measured, and should relate to the power factor of the system load.
If the three-phase voltage transformer has a broken-delta tertiary winding, then a check should be made of the voltage across the two connections from the broken delta VN and VL, as shown in Figure 3 above. With the rated balanced three- phase supply voltage applied to the voltage transformer primary windings, the broken-delta voltage should be below 5V with the rated burden connected.
Protection relay setting checks (alarm and trip settings)
At some point during commissioning, the alarm and trip settings of the relay elements involved will require to be entered and/or checked. Where the complete scheme is engineered and supplied by a single contractor, the settings may already have been entered prior to despatch from the factory, and hence this need not be repeated.
The method of entering settings varies according to the relay technology used. For electromechanical and static relays, manual entry of the settings for each relay element is required. This method can also be used for digital/numerical relays.
However, the amount of data to be entered is much greater, and therefore it is usual to use appropriate software, normally supplied by the manufacturer, for this purpose. The software also makes the essential task of making a record of the data entered much easier.
Once the data has been entered, it should be checked for compliance with the recommended settings as calculated from the protection setting study. Where appropriate software is used for data entry, the checks can be considered complete if the data is checked prior to download of the settings to the relay.
Otherwise, a check may required subsequent to data entry by inspection and recording of the relay settings, or it may be considered adequate to do this at the time of data entry. The recorded settings form an essential part of the commissioning documentation provided to the client.
Resource // Network protection and automation guide – Areva